Optimalisatie van Productieproces in de Voedingsindustrie
Uitdaging: Een middelgrote voedingsmiddelenproducent die gespecialiseerd is in verpakte snacks ondervond problemen met inefficiënte verpakkingsprocessen, wat leidde tot verhoogde productiekosten en grote hoeveelheden afval.
De bestaande verpakkingslijn was verouderd en vereiste handmatige interventies om fouten te corrigeren, wat resulteerde in inconsistente verpakkingen en falende kwaliteitsnormen.
Dit probleem bracht niet alleen de klanttevredenheid in gevaar, maar beïnvloedde ook hun concurrentievermogen in een markt die om snelle levering en hoge kwaliteit vraagt.
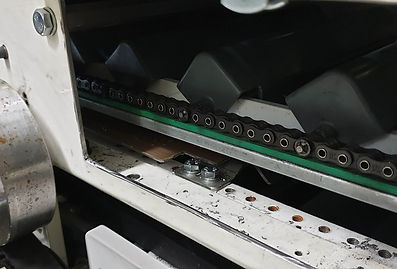

Technische en Technisch-organisatorische Aanpak van Reboow:
1.
-
Processen Onder de Loep Nemen: Reboow begon met een uitgebreide audit van de huidige verpakkingsprocessen. Dit omvatte tijd- en bewegingsstudies, evenals een analyse van foutfrequenties en afvalstromen. De audit bood inzichten in inefficiënte workflows en veelvoorkomende oorzaken van emballageproblemen.
-
Implementatie van Lean-principes: Na de analyse identificeerde Reboow gebieden waar lean-productieprincipes toegepast konden worden om de stromen en processen te verbeteren. Ze herontwierpen de verpakkingslijn om overbodige bewegingen te elimineren en de batchgrootte te optimaliseren, wat leidde tot een gestroomlijndere workflow.
-
Automatiseren en Technologische Integratie: Reboow introduceerde semi-geautomatiseerde systemen die bestaande handmatige handelingen konden ondersteunen en vervangen. Hierbij werd technologie als vision systems geïntegreerd om real-time kwaliteitscontroles uit te voeren en ervoor te zorgen dat elke verpakking aan de kwaliteitsstandaarden voldeed.
-
Operator Training en Eigenaarschap: Het personeel werd betrokken bij elk stadium van de herontwerp- en implementatiefase. Reboow zorgde voor training om medewerkers vertrouwd te maken met nieuwe systemen en processen, en creëerde feedbackloops zodat operators konden bijdragen aan continue verbeteringen.
-
Poka-Yoke Implementatie: Om menselijke fouten te minimaliseren, integreerde Reboow eenvoudige foutenpreventies (poka-yoke) zoals kleurcodes en fysieke stops in het verpakkingsproces, zodat afwijkingen direct werden opgemerkt en gecorrigeerd.
Resultaat:
De interventies van Reboow leidden tot een reductie van 25% in verpakkingsafval en een verhoging van de verpakkingssnelheid met 20%. Dankzij verbeterde procescontrole en productkwaliteit, werd de consistentie van het eindproduct verhoogd en steeg de klanttevredenheid aanzienlijk. Bovendien lukte het de voedingsmiddelenproducent om hun operationele kosten te verlagen en de winstgevendheid te verbeteren zonder grote kapitaalinvesteringen in nieuwe apparatuur.
​
Deze case illustreert hoe Reboow, door een combinatie van lean-principes en moderne automatiseringstechnieken, praktische oplossingen biedt waarmee voedingsbedrijven efficiëntieverbeteringen en procesoptimalisaties kunnen realiseren, teneinde duurzaam concurrerend te blijven.
